Partner:
Siemens Electric Machines s.r.o., Frenštát
Field: energy industry, mechanical engineering
In cooperation with experts from the Siemens company, we are pursuing development of optimal fan section design in order to improve the cooling efficiency of asynchronous electric motors. Siemens Electric Machines s.r.o., Frenštát is one of the leading producers
of low-voltage asynchronous electric motors. Their primary customers are producers of pumps, compressors, and air-conditioning equipment. One of the priorities of the Siemens company includes the production of electric motors with highly efficient cooling systems, allowing smooth operation of these machines even under extreme conditions.
If the design of the active fan section is to ensure efficient cooling of the electric motor, it is important to secure a supply of the highest possible volume of air, which is further distributed over the maximum possible surface of the electric motor frame in order to secure
sufficient exhaust ventilation of heat generated by electro-magnetic phenomena. The optimized design of the fan section shall prevent its construction from negatively affecting the running of the electric motor, which would result in an increase in mechanical losses
and excessive noise generation.
In order to find the optimal design meeting the above-mentioned parameters, tens of CFD simulations shall
be performed. Using the HPC infrastructure available at IT4I in combination with the application of an open
source software solution, CFD simulations can be performed for the whole electric motor with no shape simplifications required. Taking this approach, laboratory measurements can be fully replaced by a virtual model, which would in turn accelerate the process of designing the fan section as well as allowing the impact of each individual modification on its functionality to be assessed with no need for producing the physical prototype.
Using the IT4I infrastructure in synergy with the available know-how in CFD simulation areas, several experimentally comparable steady state and fully transient CFD simulations can be performed on a full model of the electric motor without any geometrical simplifications within two hours and two days, respectively. Simulations of one design using a common workstation, as opposed to using a state-of-the-art HPC infrastructure, takes days for steady state CFD simulations and months for a single, time-dependent CFD simulation, which makes it impossible for the design to be developed using virtual prototyping.
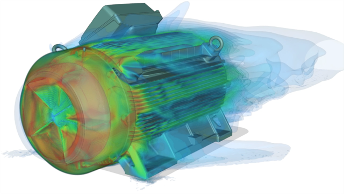
PARTNER´S NOTE
Igor Majer
Head of Research and Development Hub Ostrava
Siemens s.r.o.
“Although our cooperation with IT4Innovations National Supercomputing Center is in its early stages, we are fully aware of its potential for innovation and research projects areas. Nowadays, we can often catch buzzwords such as Industry 4.0, digitalization,
or digital twins. This particular research project successfully demonstrates that many interesting digitalization projects have been implemented in Siemens. I am firmly convinced that these joint activities not only offer great potential for increasing the competitiveness of our products but also the prospects for many
innovative solutions in the future.”